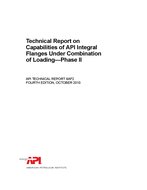
Click here to purchase
This technical report evaluates the load carrying capacity of API 6A integral flanges. The applied loading includes the end tension and bending moment in addition to the conventional rated pressure and makeup forces. The effect of a temperature difference corresponding to 250°F on the inside and 30°F on the outside is also evaluated. Three-dimensional finite element meshes are generated for each of the flanges. The computer program SESAM was used to obtain the stresses at selected critical flange and hub sections and to determine the gasket reaction due to the four unit load cases and the temperature difference load case. Leakage Criterion is defined as the load combination which reduces the initial makeup compressive forces in the gasket to zero. The stresses in each defined section are linearized in accordance with the ASME Section VIII, Division 2, procedure to determine the membrane and membrane-plus-bending stress intensities. These stress intensities are checked against the allowable conditions specified in API 6A, and the limiting loads are determined. A computer program LCCP was written to carry out this code check and a LOTUS 1-2-3 Release 3 worksheet was used to plot the load combination charts.
The three-dimensional model analysis of this study provide verification that exisymmetric finite elements results of flanges, as used in Bulletin 6AF, are conservative. Additinally, this study determined a few flanges to have lessloading capacity than originally defined in API Spec 6A for makeup loading., and thus have been reduced to meet design requirements.
Product Details
- Edition:
- 4th
- Published:
- 10/01/2010
- Number of Pages:
- 118
- File Size:
- 1 file , 7.4 MB
- Redline File Size:
- 2 files , 15 MB
- Product Code(s):
- G, G6AF24, G6AF24, G, G, G6AF24
- Note:
- This product is unavailable in Cuba, Iran, North Korea, Syria